Với sự ra đời của đo lường thông minh, đã dần thay thế các phương pháp kiểm soát chất lượng truyền thống cũ, lỗi thời, giảm những lỗi sai sót trong quá trình sản xuất.
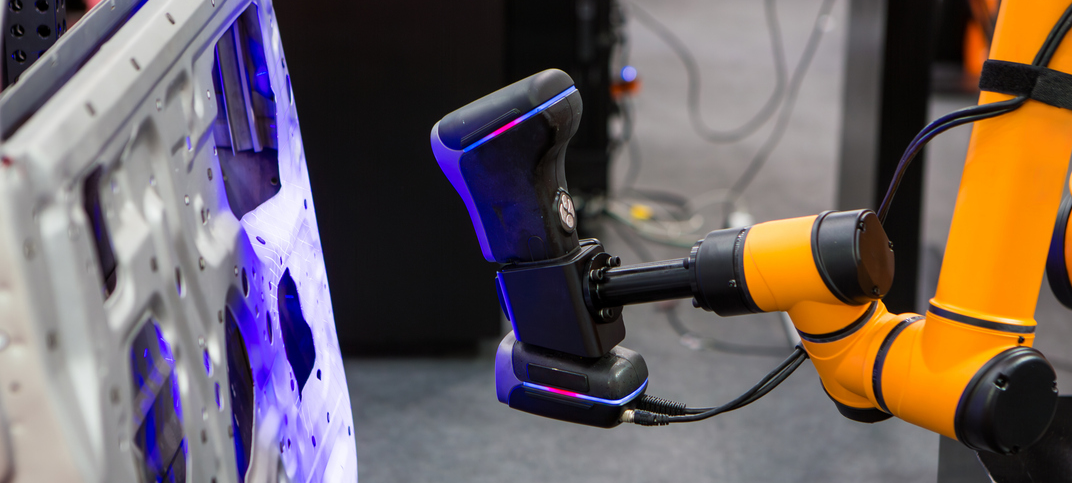
Kiểm soát chất lượng luôn là nền tảng của sản xuất, đảm bảo rằng sản phẩm đáp ứng các tiêu chuẩn nghiêm ngặt và kỳ vọng của khách hàng. Theo truyền thống, kiểm soát chất lượng bao gồm kiểm tra thủ công, lấy mẫu và đo lường ngoại tuyến, mặc dù hiệu quả trong nhiều trường hợp, nhưng lại tốn thời gian, dễ xảy ra lỗi và thường mang tính cảm tính hơn là chủ động. Tuy nhiên, với sự ra đời của đo lường thông minh (Smart Metrology), việc kiểm soát chất lượng có thể đạt kết quả tốt hơn nhất là khi áp dụng các công nghệ, cách tiếp cận truyền thống sẽ dần bị thay thế.
Đo lường thông minh tích hợp các công nghệ kỹ thuật số tiên tiến như Internet vạn vật (IoT), trí tuệ nhân tạo (AI), phân tích dữ liệu lớn và điện toán đám mây vào các quy trình đo lường, giúp chúng hiệu quả hơn, chính xác hơn, thông minh hơn và nhanh chóng hơn. Đo lường thông minh đang cách mạng hóa kiểm soát chất lượng truyền thống trong sản xuất, dẫn đến một phương pháp chủ động hơn, dựa trên dữ liệu, không chỉ đảm bảo chất lượng mà còn thúc đẩy cải tiến liên tục.
Những hạn chế của kiểm soát chất lượng truyền thống
Những hạn chế của quy trình kiểm soát chất lượng thông thường thường dựa vào việc kiểm tra và lấy mẫu định kỳ. Sản phẩm được thử nghiệm ở các giai đoạn cụ thể của dây chuyền sản xuất và các phép đo được thực hiện bằng các công cụ thủ công hoặc bán tự động. Sau đó, các phép đo này được so sánh với các tiêu chuẩn chuẩn mực để xác định xem sản phẩm có đạt hay không.
Mặc dù cách tiếp cận truyền thống này đã trở thành ứng dụng tiêu chuẩn trong nhiều thập kỷ, nhưng so với thời đại công nghệ số hiện nay đã này sinh một số hạn chế:
Bản chất phản ứng: Kiểm soát chất lượng truyền thống thường mang tính phản ứng. Các vấn đề thường được xác định sau khi chúng xảy ra, nghĩa là các sản phẩm lỗi có thể đã có trong hệ thống trước khi phát hiện ra vấn đề.
Lỗi lấy mẫu: Việc kiểm soát chất lượng truyền thống trước đây hầu như đều dựa vào việc lấy mẫu, rất ít khi kiểm tra từng sản phẩm riêng lẻ. Tuy nhiên, việc lấy mẫu có nguy cơ xảy ra lỗi vì không phải tất cả các lỗi đều có thể được phát hiện trong mẫu dẫn đến sự thay đổi về chất lượng sản phẩm.
Tốn thời gian: Kiểm tra và đo lường thủ công tốn nhiều công sức và thời gian. Chúng có thể tạo ra tình trạng tắc nghẽn trong quy trình sản xuất, làm chậm năng suất chung.
Dữ liệu thời gian thực không chuẩn xác: Các phương pháp kiểm soát chất lượng truyền thống thường liên quan đến các phép đo ngoại tuyến, nghĩa là dữ liệu không có sẵn theo thời gian thực. Việc phản hồi kết quả bị gián đoạn khiến việc điều chỉnh nhanh chóng các quy trình sản xuất để ứng phó với các vấn đề về chất lượng trở nên khó khăn.
Những hạn chế này tạo ra thách thức cho các nhà sản xuất, đặc biệt là trong các ngành công nghiệp mà độ chính xác, tốc độ và tính nhất quán là tối quan trọng. Đây là lúc đo lường thông minh phát huy tác dụng, cung cấp một phương pháp tiếp cận mang tính chuyển đổi đối với kiểm soát chất lượng, giải quyết trực tiếp những thách thức này.
Vai trò quyết định của đo lường thông minh trong quá trình kiểm soát chất lượng
Bằng cách tích hợp các thiết bị được kết nối, phân tích dữ liệu, AI và tự động hóa vào quy trình đo lường, đo lường thông minh chuyển đổi kiểm soát chất lượng từ quy trình thủ công, phản ứng thành quy trình chủ động, tự động.
Giám sát và thu thập dữ liệu theo thời gian thực: Một trong những lợi thế quan trọng nhất của đo lường thông minh là khả năng giám sát và thu thập dữ liệu theo thời gian thực. Trong hệ thống, các thiết bị đo lường được trang bị cảm biến IoT liên tục thu thập dữ liệu trong quá trình sản xuất. Dữ liệu này sau đó được truyền đến hệ thống trung tâm, nơi dữ liệu có thể được phân tích ngay lập tức.
Giám sát theo thời gian thực có nghĩa là kiểm soát chất lượng không còn giới hạn ở các cuộc kiểm tra định kỳ. Thay vào đó, các phép đo được thực hiện liên tục, cung cấp luồng dữ liệu liên tục về chất lượng sản phẩm. Điều này cho phép các nhà sản xuất phát hiện các vấn đề khi chúng xảy ra, thay vì sau đó. Ví dụ, trong ngành công nghiệp ô tô, việc giám sát theo thời gian thực các thành phần trong quá trình lắp ráp có thể xác định ngay các sai lệch so với thông số kỹ thuật, cho phép điều chỉnh ngay lập tức và ngăn chặn các bộ phận bị lỗi tiến triển xa hơn trong dây chuyền.
Kiểm soát chất lượng dự đoán: Kiểm soát chất lượng truyền thống chủ yếu là phản ứng, các vấn đề được giải quyết sau khi chúng đã được xác định. Ngược lại, đo lường thông minh cho phép chuyển sang kiểm soát chất lượng dự đoán. Bằng cách phân tích dữ liệu lịch sử và thời gian thực bằng AI và thuật toán học máy, các hệ thống có thể dự đoán các vấn đề chất lượng tiềm ẩn trước khi chúng xảy ra.
Hệ thống phản hồi vòng kín: Đo lường thông minh tạo điều kiện thuận lợi cho việc triển khai hệ thống phản hồi vòng kín trong sản xuất. Trong hệ thống vòng kín, dữ liệu đo lường được đưa trở lại quy trình sản xuất để liên tục tối ưu hóa hoạt động. Điều này tạo ra một hệ thống năng động, tự hiệu chỉnh, trong đó chất lượng luôn được duy trì ở mức cao nhất.
Khả năng truy xuất nguồn gốc và tuân thủ được cải thiện: Trong các ngành công nghiệp có yêu cầu quản lý nghiêm ngặt, chẳng hạn như hàng không vũ trụ hoặc thiết bị y tế, khả năng truy xuất nguồn gốc và tuân thủ là rất quan trọng. Đo lường thông minh tăng cường khả năng truy xuất nguồn gốc bằng cách cung cấp hồ sơ kỹ thuật số về mọi phép đo được thực hiện trong quá trình sản xuất. Dữ liệu này có thể được lưu trữ trên đám mây, đảm bảo rằng dữ liệu có thể dễ dàng truy cập để kiểm toán, kiểm tra tuân thủ và đánh giá chất lượng.
Ví dụ, trong ngành hàng không vũ trụ, nơi mọi thành phần phải đáp ứng các tiêu chuẩn khắt khe, hệ thống sẽ cung cấp một bản ghi kiểm toán kỹ thuật số toàn diện. Điều này bao gồm các hồ sơ chi tiết về từng phép đo, các điều kiện thực hiện phép đo và bất kỳ điều chỉnh nào được thực hiện. Khả năng truy xuất nguồn gốc được nâng cao không chỉ đơn giản hóa việc tuân thủ mà còn giúp các nhà sản xuất nhanh chóng xác định và giải quyết các nguyên nhân gốc rễ của các vấn đề về chất lượng.
Nguồn: Theo VietQ.vn